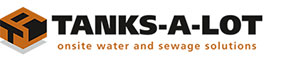
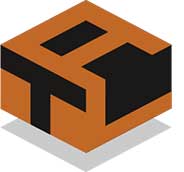
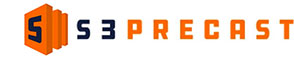
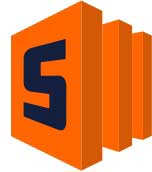
BHP Jansen
BHP Jansen Stage 1 is a potash project located in the province of Saskatchewan. Located in the world’s best potash basin, BHP Jansen is planned to be the largest potash producing mine in the world and is expected to operate up to 100 years. The large resource endowment provides the opportunity to develop Jansen in phases, with anticipated initial capacity of 4.35 megatonnes per annum (Mtpa) of potash when the project becomes operational in 2026.
Our Solution
Working in conjunction with Trenwa Precast Trench Solutions, we supplied approximately 430 H40 traffic-rated precast concrete trenches for power and communication cables installed at the BHP Jansen mine site. Each piece measured 3.05m long, 1.83m wide and 0.91m tall.
Features & Benefits
Concrete Fence for Manning Village
Designed around the concept of a village with convenience and community in mind, Manning Village is a residential development by Cameron Communities in Edmonton’s northeast. In laying out the design for the neighbourhood, the developers envisioned a community that drew on traditional architectural elements while addressing the needs of contemporary living using modern building materials. Cameron Communities identified the need for a visual barrier for a portion of the homes backing onto the stormwater pond. In keeping with the community’s design guidelines, the material required for the barrier had to be selected for maximum durability and minimum maintenance.
Our Solution
We worked with the consulting engineer on several concepts and ultimately selected our concrete fence with the Sierra/Durango stone texture. Our concrete fence enables custom textures that mimic the look and feel of stone masonry – a key deciding factor. The end result was a visually stunning concrete fence that provided privacy while staying true to the neighbourhood’s design guidelines.
Construction
We designed and supplied approximately 165m of concrete wall between 8 and 10 foot heights.
Features & Benefits
Introduction to Precast Concrete Walls
Precast concrete walls offer a durable, flexible and aesthetically-pleasing solution for noise abatement and other applications. These properties were well-highlighted on the St. Albert Barrier Wall Replacement project.
The St. Albert Barrier Wall is a stretch of concrete wall that serves as a visual and noise barrier for residents along St. Albert Trail. Constructed between 1983 and 1992, the existing wall needed to be replaced after an independent assessment identified structural concerns and a loss of effectiveness of the wall’s sound attenuation. As such, the third-party’s recommendation was for a full replacement of the existing wall between Giroux Road and Sturgeon Road along St. Albert Trail.
As part of the evaluation process, the City of St. Albert considered multiple bids across varying materials – wood, composite, concrete, metal – but ultimately selected our precast concrete wall solution. Our team successfully carried out the project in three phases between 2018 and 2020.
Our Solution
The City opted for our concrete wall thanks to its durability, longevity, ease of installation and noise attenuation properties. Concrete is inherently more durable, more forgiving and longer-lasting. Concrete also has superior noise abatement characteristics when compared against other materials. Additionally, our ability to produce longer span walls of 4.88m (16 feet) at 5.23m post-to-post spacing requires less piles and posts, thereby resulting in reduced costs and an improvement to the project speed.
Construction
Phase 1 (2018) – Portion of wall between Giroux Road and Villeneuve Road. Total length of 300m across panel height of 7 feet
Phase 2 (2019) – Portion of wall between Hebert Road and Sterling Street. Total length of 850m across panel heights of 8 and 16 feet
Phase 3 (2020) – Portion of wall between Sterling Street and Sturgeon Road. Total length of 900m across panel heights of 8 and 16 feet
Features & Benefits
Problem
Stormwater tanks are an excellent solution for onsite stormwater storage – a growing challenge for cities as they grapple with urban sprawl. With the increase in appetite for transit and pedestrian-oriented living, Rohit Commercial developed Stadium Yards, a new 7 acre mixed-use urban village situated next to Edmonton’s Stadium LRT Station. The development will welcome an additional 1500-2000 residents to Edmonton’s core with a commercial main street and parks. The developer wanted a solution for a stormwater tank that maximized volume capacity without sacrificing land for development.
S3 Precast Solution
We designed and supplied precast, modular 1800mmx1800mm (6′ x 6′) traffic-rated concrete box sections connected together to achieve the desired storage volume of 84m3 (18,500 gallons). As a result, the developed could salvage valuable land above the stormwater tank. In addition, we also performed onsite assembly of the units. We utilized our proprietary, industry-leading best practices of sealing the joints using post-tension wire, thereby ensuring a watertight seal. The video included above illustrates the ease of use and the modular design of our proposal. A similar project was completed previously in Sherwood Park.
Construction
We fabricated 11 precast box sections at our new 90,000 sq. ft. production facility located in Edmonton in under 2 weeks. Onsite assembly was completed over 2 days.
Features & Benefits
Problem
Alberta Parks and Parks Canada are in the process of providing a face lift to a majority of aging provincial parks infrastructure. Part of this process involved replacing a majority of the existing washroom/outhouse structures which were in a poor state of disrepair or had aged enough beyond repair. Majority of the builds to be replaced were ranged from 15 – 30 years old, in addition to the age, all the replaced buildings were constructed of wood which meant weathering and the elements took their toll on the structures resulting in the uneven appearance of materials and overall finished look across many.
TAL Solution
In order to maintain a quality experience for the parks visitors, these new facilities had to be universally accessible, be designed for high traffic, be vandalism-resistant, easier to clean and help cut down on maintenance costs. In addition to the quality and safety characteristics, all the precast concrete washrooms had to be aesthetically pleasing and match other concrete buildings which had been replaced already around the park. To protect against vandalism and maintain the look of the buildings, both the interior and exterior surfaces had to be protected with a clear anti-graffiti coat.
Construction
Tanks-A-Lot prides itself in delivering as turn key solutions as possible to minimize site assembly and handling time making it easier for generals to work with our products and solutions. This project was no different. To minimize handling and site assembly time all the precast modular pieces were produced indoors and stored indoors until they fully cured upon which they were stained to the desired finish and shipped to site for assembly. This minimize site disturbance, time on site and eliminates the need for lay-down areas as the whole unit can be assembled straight from the deck of a truck.
Features & Benefits
Problem
Redevelopment and infill are strategies for mitigating urban sprawl in growing cities. This redevelopment strains existing stormwater infrastructure which forces new and innovative solutions. The redevelopment of the Sherwood Park Mall gave an opportunity to protect the existing municipal stormwater infrastructure by preventing stormwater backups to not only the mall but the residences of the surrounding area during severe weather events.
TAL Solution
Stormwater ponds are the typical solution for stormwater buffering on sites without land constraints. With no space to construct a stormwater pond at a mall but plenty of area for parking, an underground solution to temporarily store this stormwater would be ideal. The TAL solution was a 2.4 meter square by 49 meter long precast concrete tank below the parking lot to store stormwater coming in through 2 – 200mm inlets, slowly released through 1 – 150mm outlet. This significantly reduced the strain on the existing stormwater system by storing over 250 cubic meters of stormwater from entering the municipal system all at once.
Construction
The design consisted of 2 end castings and 13 ring sections, each section sealed with 2 layers of butyl rubber sealant in the overlap joints. These sections were fastened together using continuous tensioned steel cables to provide a uniform compression in these joints and sealant. Being a precast solution, the onsite time was less than 3 days from time of open excavation to backfill and was essential in mitigating scheduling and site risk. With mall parking spaces at a premium, it was a requirement that the structure be CL625 traffic rated, which was achieved with a high performance concrete having the CAN-CSA A23.1, S3 rating and steel reinforcement.
Features & Benefits
Problem
Midwest Pipeline Contractors established new premises in Spruce Grove AB, adjacent to Highway 788 also known as Saskatchewan Avenue. Being situated along such a prominent location and along a major roadway in and out of the City of Spruce Grove meant most of their site activity was in plain view.
Given the huge inventory of expensive mining equipment and parts found on the yard at any given time, going the chain-link route was not an option as it did not keep out onlookers and presented maintenance and security challenges as it could easily be breached. Wood screen was also considered as an option but was quickly discarded based on short service life and the effects weathering would have on it over time.
TAL Solution
2.4-meter height fence was constructed in 2015 along approximately 250 lineal meters of berm to provide privacy, security and aesthetics to the business. Not only did our solution enhance the profile of the business within the community, we were able to meet and exceed all of the client’s three primary concerns (security, privacy and high aesthetics). As with all TAL Stone Fence installations, the new fence provided the client with the highest service life and lowest cost cycle for maintenance of any fencing material on the market.
Construction
All the posts and panels were prefabricated at our plant in North East Edmonton prior to shipping and installation.
Features & Benefits
Problem
A precast concrete sound wall was constructed for the new Cavanagh Community, a partnership between some of Edmonton’s biggest land developers – Cameron Developments, MacLab Developments and Melcor. A huge portion of the land backed directly onto Highway 2 – a major highway connecting Edmonton and Calgary. As a result, the City required the developers to construct a sound wall to buffer and protect the community from noise levels generated by the high traffic volumes.
The developers considered Double-boarded wood screen, Masonry/Allan Block, Vinyl, and Recycled PVC walls. However, these were either too expensive or had a shorter service life. Therefore, precast concrete offered the best solution for this project.
TAL Solution
A 3.0-meter height sound wall was constructed in 2015 along approximately 500 lineal meters of berm to provide sound protection, privacy and aesthetics to the Cavanagh Community. Fully built, the wall will encompass 2500 square meters of fencing, including approximately 1500 square meters constructed in 2015.
Construction
We prefabricated all the posts and panels at our plant in NE Edmonton. Posts and panels were erected to their in-service position directly from the delivery trucks (Super B’s). As such, we were able to erect approximately 100 linear meters per day and be on and off the site within a couple of days.
Features & Benefits
The Problem
The Town was looking to replace the west and east entrance Town of Bon Accord welcome monuments signs which were becoming dilapidated and past their service lives. The Town wanted replacement signs which would incorporate elements of the old sign, be of high aesthetic value and be durable.
TAL Solution
For the design, we wanted to present a sign that would embody a strong sense of community, preserve elements and connections to the Town’s predominately Scottish Heritage as well as improve the sense of arrival and place for residents, visitors and motorists passing the Town on HWY 28.
By combining our Verti-Crete Architectural Precast system with some ornamental wrought iron elements produced by Behrends not only we were able to preserve elements of the old sign, we were able to also deliver on the three key elements the sign had to meet, which are:
Problem
The town of Claresholm wanted to install two additional lift stations to service a new planned 50 home and commercial subdivision. The consultant initially considered a 2400mm diameter fiberglass lift structure which presented a number of challenges. For one, the area in question had unusually high water tables which presented some buoyancy challenges. In addition, using a fiberglass product complicated site dynamics and soils management. A bigger excavation would be required and structured materials would have to be hauled in for back fill. In addition, the excavated soils would have to be hauled away for disposal elsewhere which would negatively impact the overall installed cost.
TAL Solution
Our solution was a 2.4m x 2.4m diameter x 6.4m height square precast concrete lift station which kept the same design guidelines as the fiberglass product that had been originally specified. Going this route eliminated concerns of buoyancy as the weight of the concrete castings alone was enough to overcome any buoyancy issues. Our precast concrete solution also improved the site dynamics and soils management concerns as all the excavated materials remained on site and were used for back fill, eliminating the need to haul those materials away and to haul in engineered materials for back fill. All this meant that the overall installation cost of the project was lower by at least 30 – 40% over the fiberglass product.
Construction
It took a total of 5 weeks from the time we fabricated the first piece to the time the project was complete. Onsite assembly of the lift station took less than 6 hours.